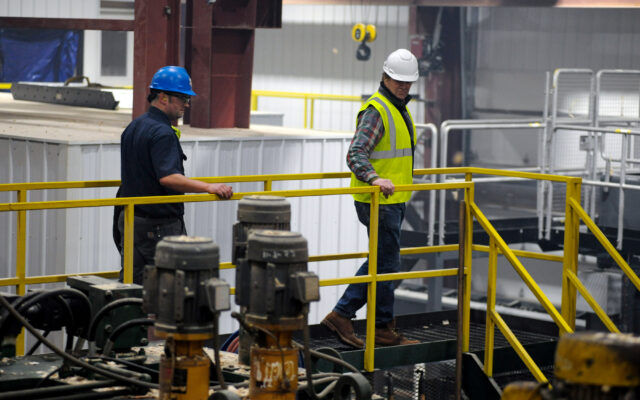
A Maine factory is selling a new product to get PFAS out of crops
By Lori Valigra, Bangor Daily News Staff
A new twist on an ancient agricultural practice is playing out at farms throughout Maine and the nation.
Biochar, a charcoal-like substance made from heated organic biomass such as forest and agricultural waste, is the subject of several research studies now underway on Maine farms. When added to tainted soil, it is showing promise in reducing the uptake of forever chemicals in crops, researchers said. It can store water that it then releases during droughts. And it can increase nutrient retention in soil and boost carbon sequestration, according to the American Farmland Trust.
If the current research tackling those huge challenges to the food supply bear fruit, the market for biochar could boom. And Maine is getting ready for that.
In October, the second biochar producer in the state started commercial production. Standard Biocarbon is producing 50 cubic yards of biochar a day, said Fred Horton, a co-owner of the company. Standard Biocarbon’s factory in Enfield, in Penobscot County, claims to produce organic biochar that is clean, so it doesn’t further pollute farm fields already contaminated by per- and polyfluoroalkyl substances, or PFAS, he said.
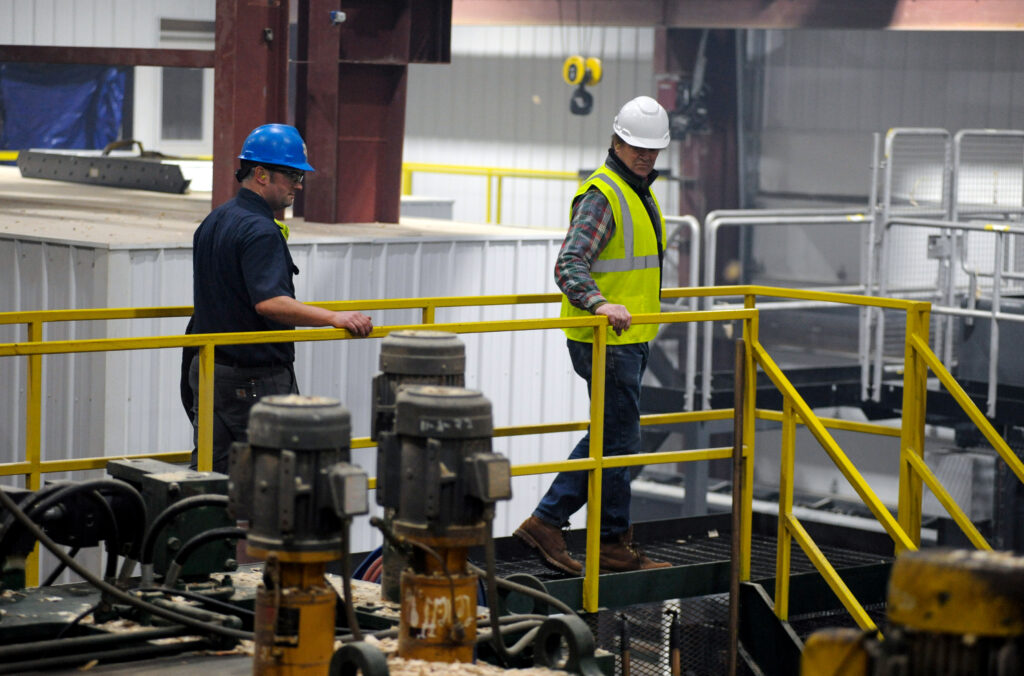
BIOMASS SOURCING — Michael LeBrun, left, general manager of Pleasant River Lumber’s Enfield mill, and Fred Horton, a co-owner of Standard Biocarbon, walk a catwalk above the saw as logs move through in this January 2023 file photo. Standard Biocarbon is sourcing biomass from Pleasant River to make biochar, a charcoal-like substance that can be used as a soil amendment to trap and hold forever chemicals.
PFAS, which have been found in sludge spread on farm fields across Maine in the 1980s and 1990s, have been linked to kidney and testicular cancers and low birth weight in humans.
“Biochar is very much like activated carbon to filter out heavy metals, arsenic, lead and other toxins in soil,” Horton said.
The other biochar maker, Clean Maine Carbon of Greenville, started producing 20 cubic yards a day in June 2023. That’s enough to fill a tractor trailer every three days. The biggest use of its product is in agriculture to enrich soil by increasing its carbon content, company President Pat Jones said. The factory is located in the former Greenville steam plant.
Farmers in South America’s Amazon River basin created charcoal-rich soil similar to today’s biochar more than 2,500 years ago, but today’s biochar is made with modern equipment that enhances its absorptive qualities.
In Maine, biochar is already produced as a byproduct at power plants, but it can have high traces of heavy metals, which are bad for soil. Standard Biocarbon added some quality control measures, first by sourcing its biomass from nearby Pleasant River Lumber, a sawmill that cuts spruce and fur logs into dimensional lumber. Standard Biocarbon uses high-temperature kilns to remove impurities in the wood.
The company produces biochar through a process called pyrolysis, which involves high temperatures and the absence of oxygen. Horton said the company bought the first biochar production machine in the United States made by the German company PYREG. The two-story high machine has three main components: the reactor chamber, furnace and filter.
The furnace is first fired up with propane until the wood chips shed a biogas, called syngas, which is sucked out through a ceramic filter. The material continues to burn at about 2,900 degrees Fahrenheit. The wood chips move through an airlock chamber to keep out oxygen until mostly carbon is left. The end product is biochar, which Horton said is 90 percent carbon.
The finished product looks like dark mulch chips. It is very porous, so it can sequester PFAS. A lot of research still needs to be done to see how effective biochar can be, how long it will hold onto PFAS, how much is needed on a field and how often it needs to be added to soil, Horton said.
“The hope is that a single application can interrupt the uptake permanently, but, again, this is part of what needs to be studied and confirmed,” he said.
Jones of Clean Maine Carbon said the adoption of biochar is not happening as quickly as people had expected. So far, the companies have been selling directly to agricultural clients and research projects, but individuals can buy small bags directly from the companies. Some big-box stores such as Home Depot and Lowe’s sell small bags of biochar or biochar mixed in with compost for home gardeners.
“If you put biochar down on your field, now you’ve got to wait another year before you know what happened,” Jones said. “It’s not something where you instantaneously see the benefits.”
Investors also want to see benefits before funding new biochar companies or projects. Horton already has raised the money to cover his more than $10 million in capital expenditures so far, but he continues to work on funding. Without strong demand, biochar will be too expensive, and it will be tough to create a market for it, he said.
A U.S. Department of Agriculture incentive program subsidizes the use of biochar for farmers to improve their soil, but it reimburses at about $200 per cubic yard, so farmers are unlikely to buy from any company selling it at a higher price, Horton said.
“The price to a farmer has to be essentially zero, or they won’t use it, no matter how well it works,” Horton said.
That, along with additional research needed to support the expected benefits of biochar, have set a high bar for the promising new market. To attract investors, the companies need to prove biochar works, but they also need the funding to produce the biochar to be tested.
“They’ve got to prove with research that it works,” said Keith Hunter, owner of Little Darling’s Dairy in Unity, whose cows have been contaminated by PFAS-tainted feed. “If it works, and it works long term, then funding will probably come along.”
Valigra is an investigative environment reporter for the BDN’s Maine Focus team. She may be reached at lvaligra@bangordailynews.com. Support for this reporting is provided by the Unity Foundation, a fund at the Maine Community Foundation, and donations by BDN readers.